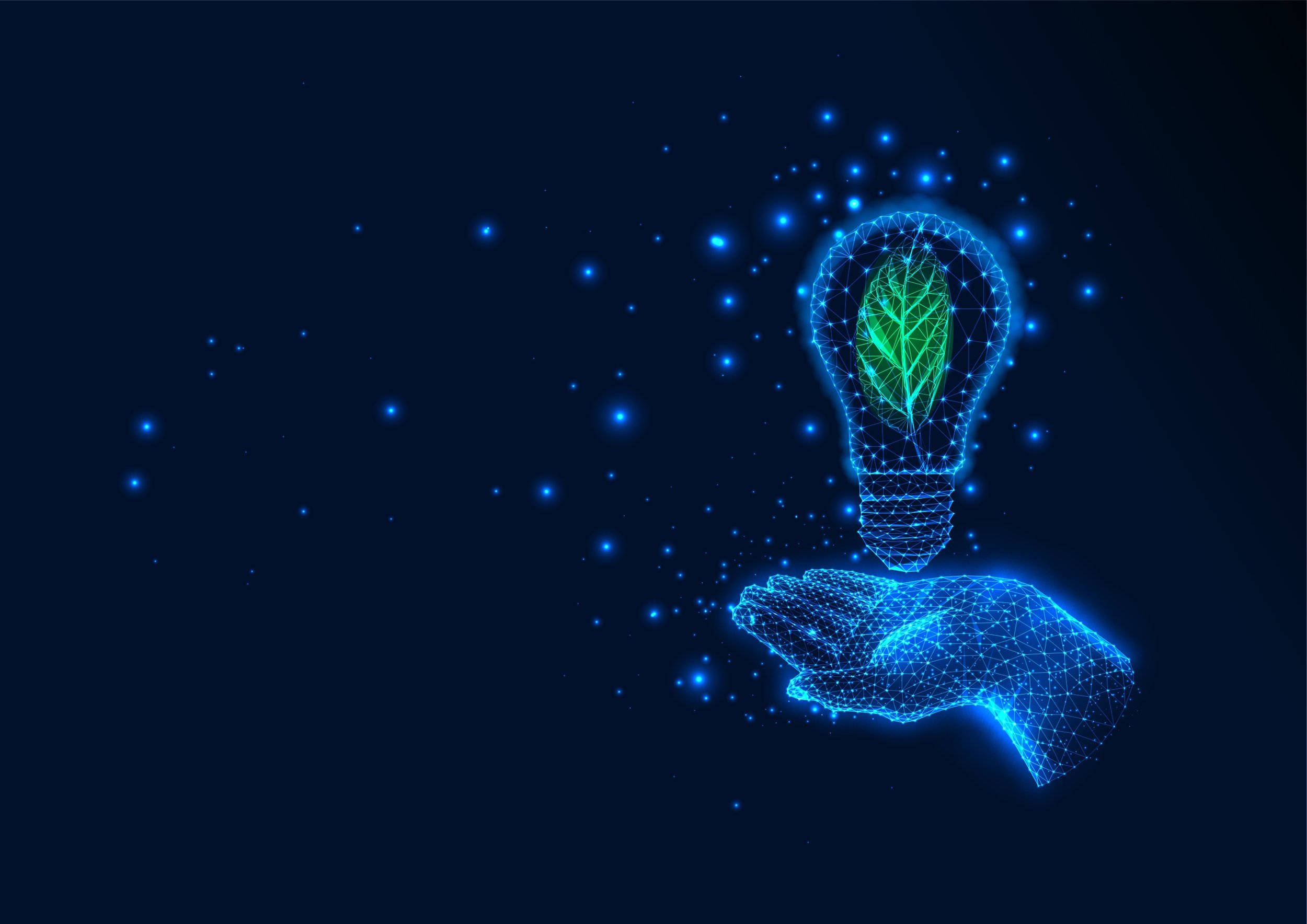
SOLUTIONS
Energy storage
Graphite is the single largest component of a lithium-ion battery, contributing to over 30% of total battery weight. We’re developing a wide range of graphite anode materials suitable for use in all types of lithium-ion batteries.
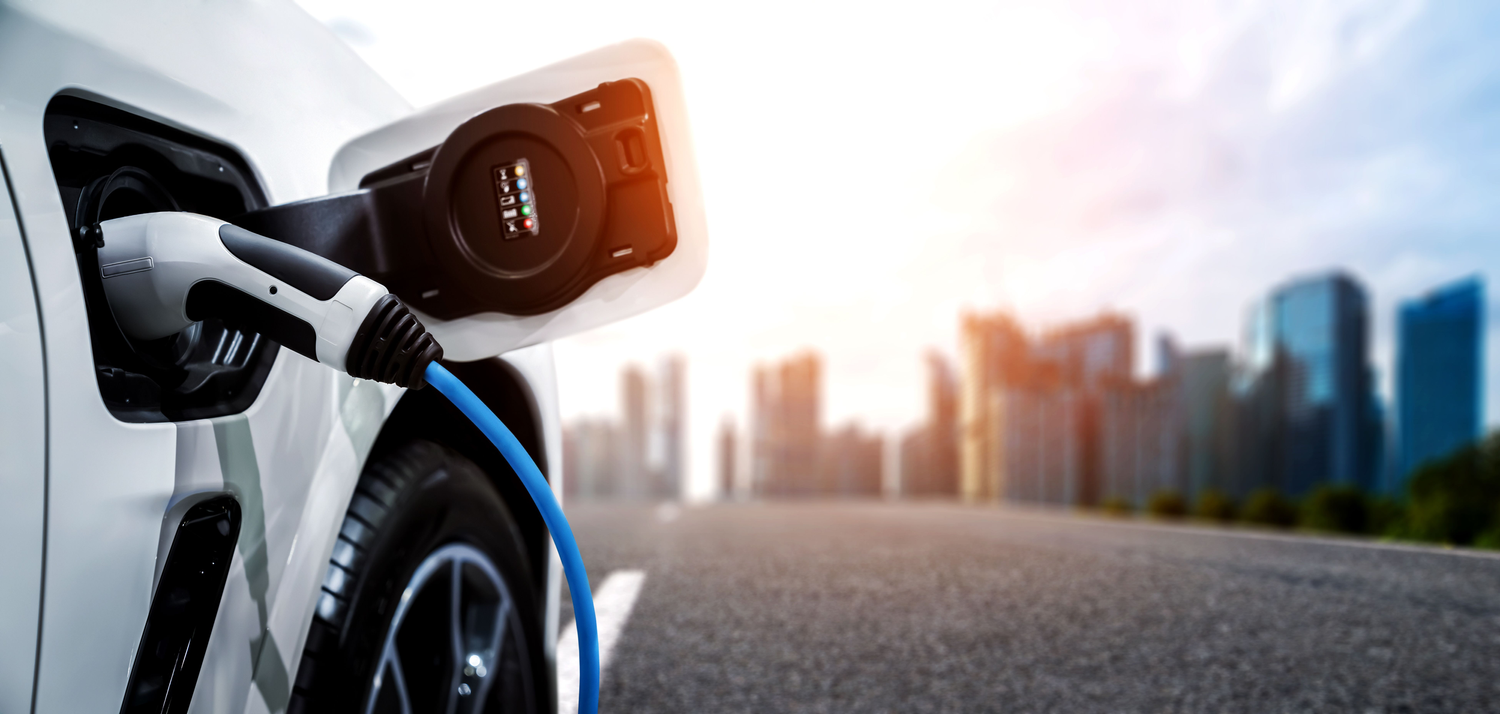
Electric vehicles
The average electric vehicle battery contains 160 lbs of graphite anode material. In order to reach full EV adoption, the graphite anode material market will need to grow from 1 million tons per year to 19 million tons per year.
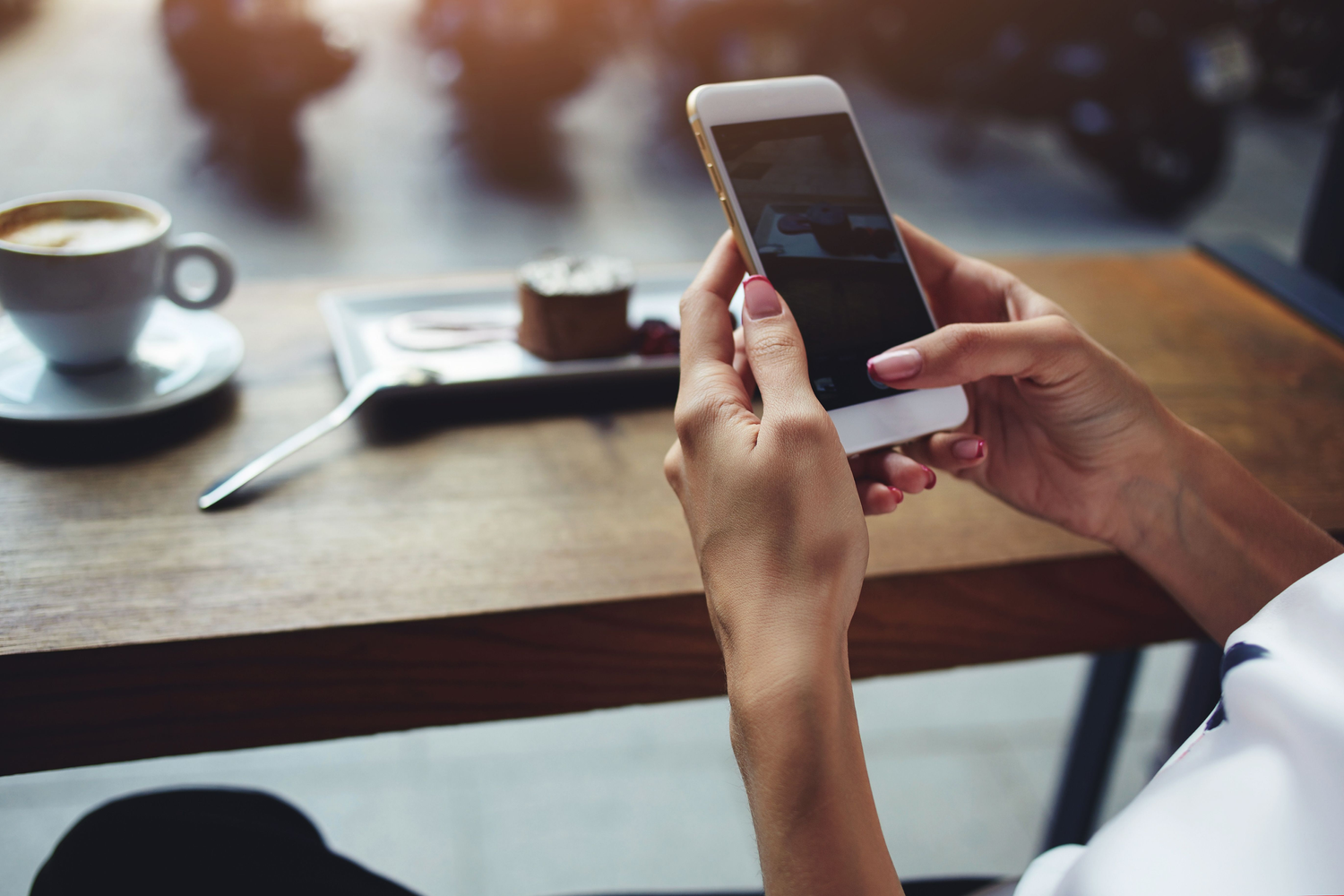
Consumer electronics
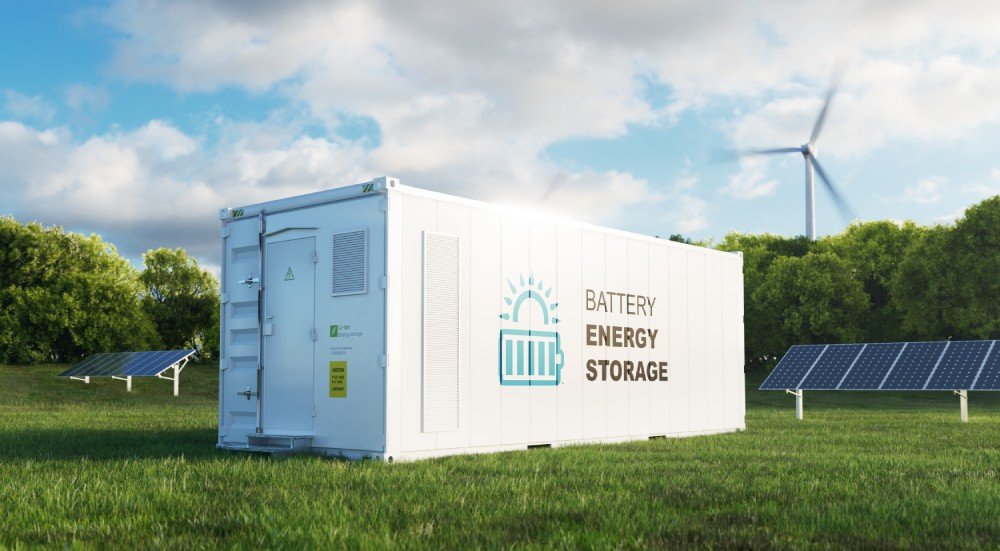
Grid storage
Solar energy is now cheaper than coal, but only during the day. According to the IEA, Installed grid-scale battery storage capacity needs to expand 35-fold by 2030 to reach Net Zero Emissions by 2050. Lithium-ion batteries make up the majority of all new grid storage deployments and are key to reducing the levelized cost of intermittent renewable energy sources like wind and solar.
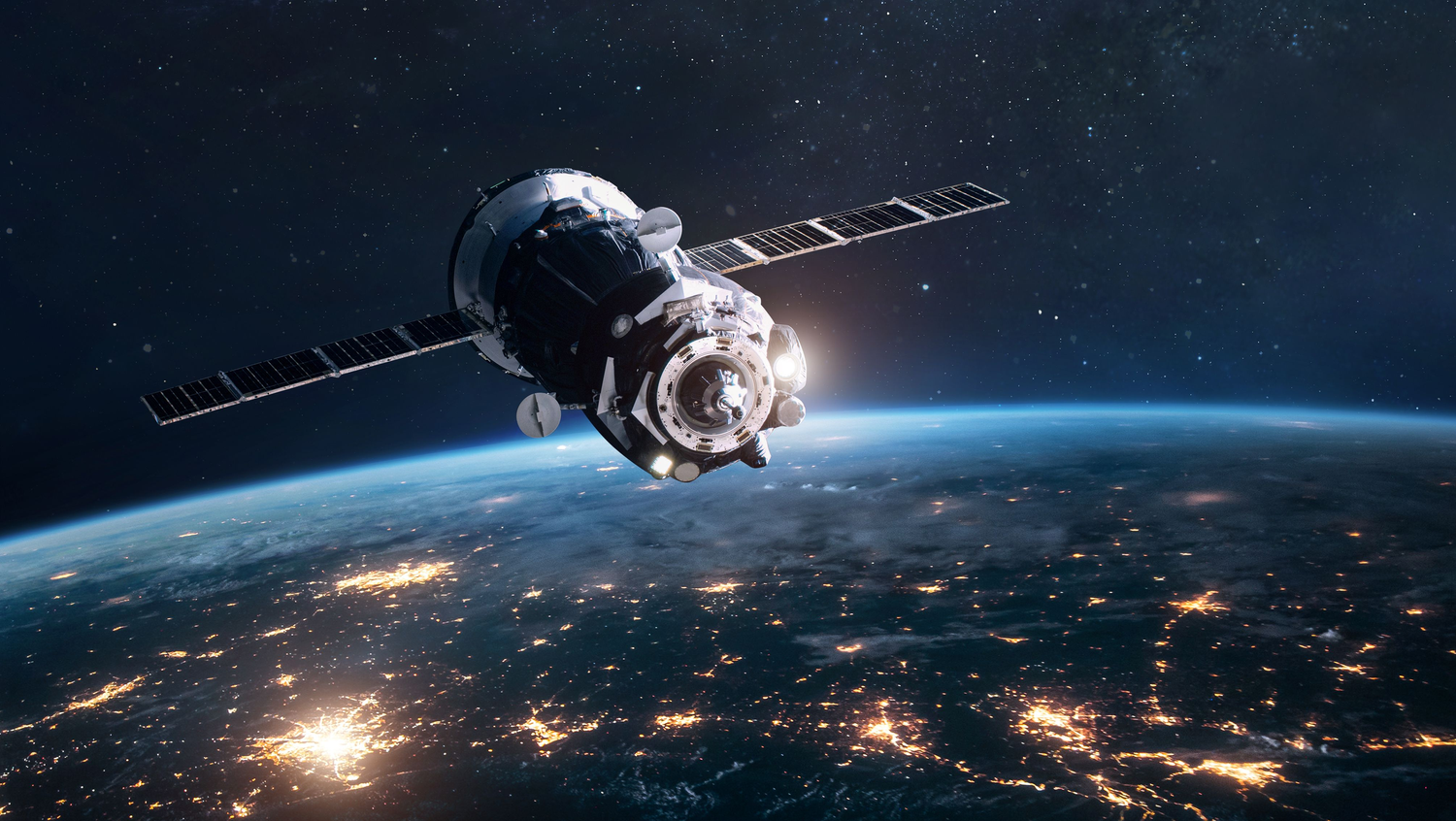
Aerospace & Defense
The United States accounts for less than 1% of global graphite anode material production. The current process for manufacturing artificial graphite anode materials from oil is dominated by suppliers in the Asia-Pacific region and domestic reserves of natural graphite are virtually non-existent. The need to rely on foreign-sourced battery supply chains puts the economic and national security of the United States at considerable risk.
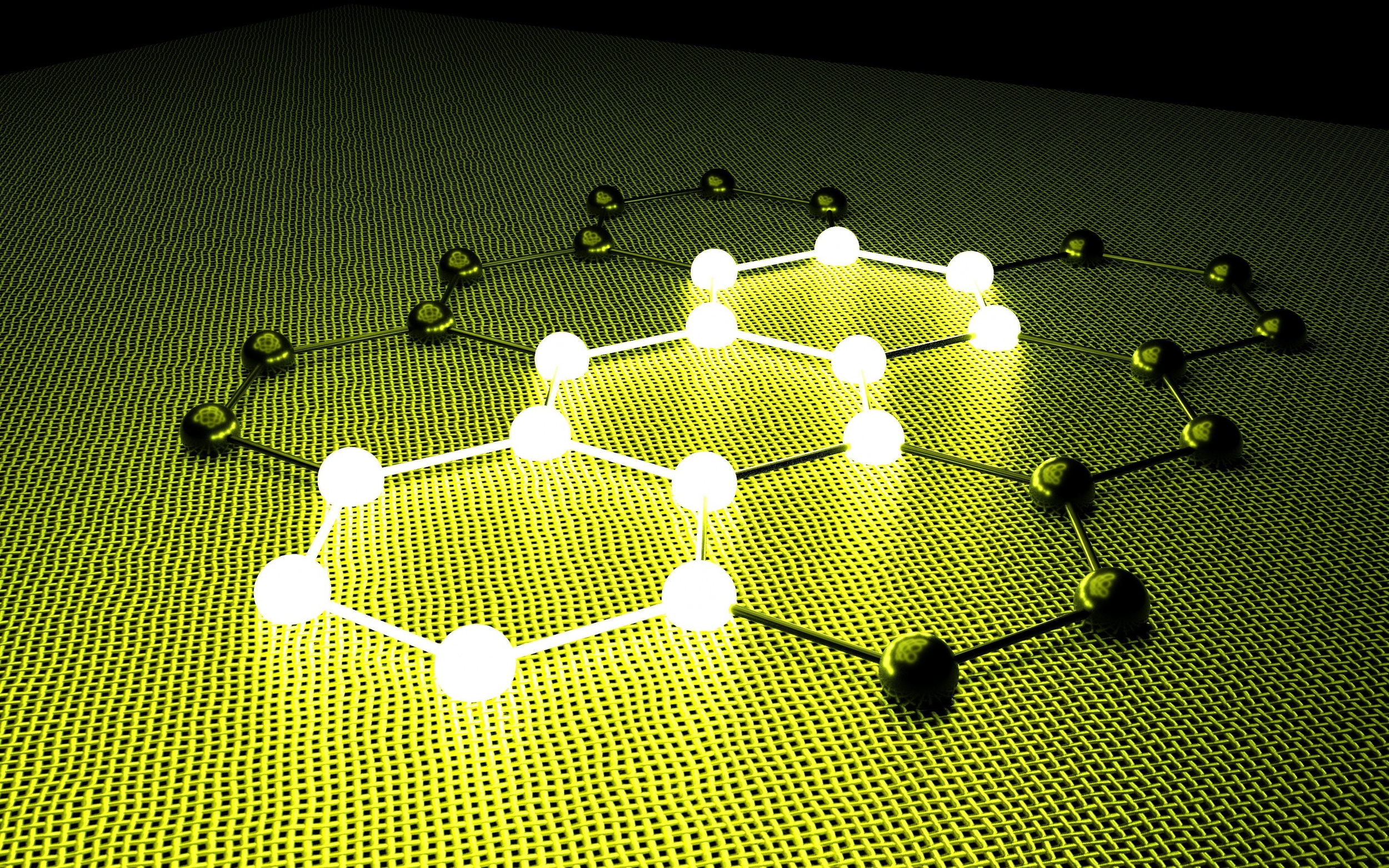
Industrial Decarbonization
The industrial sector accounts for 31% of global greenhouse gas emissions. Learn more about new product lines we’re developing to support industrial decarbonization and the circular economy.
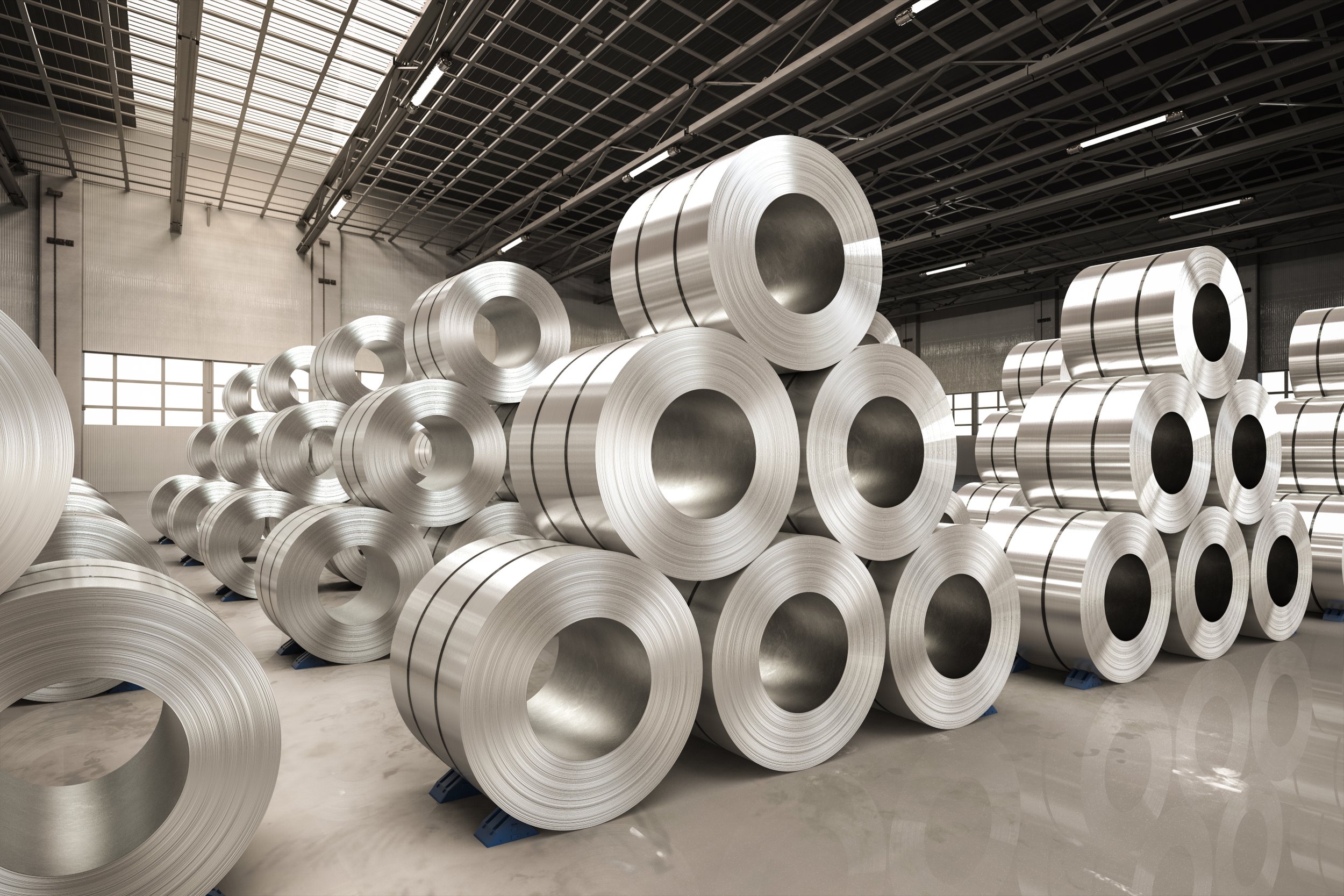
Next Generation Aluminum
Aluminum smelters use carbon anodes that release CO2 as a part of the electrolysis process. In 2022, the aluminum industry contributed to 3% of the world’s direct industrial CO2 emissions. Ironically, CO2 emissions produced by the aluminum industry are steadily increasing as a greater number of vehicles, both gas and electric, replace heavy steel components with aluminum to reduce weight and increase fuel economy.
Maple Materials is developing a proprietary formulation of high-conductivity, CO2-derived carbons to be used as a drop-in replacement for conventional petroleum cokes used in today’s aluminum smelters.
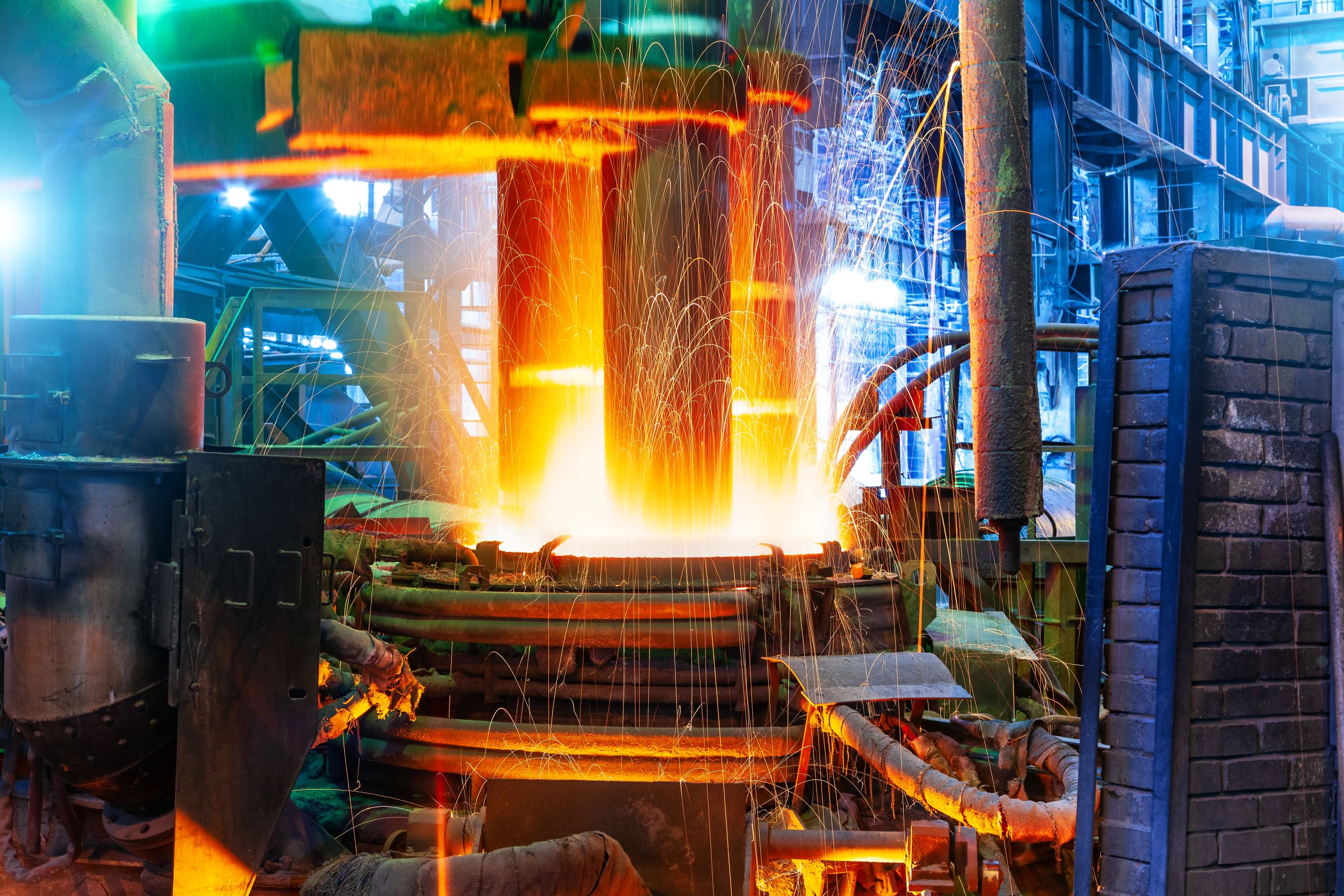
Green Steel
EAF steelmaking is the largest end use for graphite globally and accounts for 70% of US iron and steel production. During the EAF steelmaking process, specialized graphite electrodes are used to heat and melt scrap steel by means of an electric arc. This rapidly growing manufacturing technology enables the electrification of steel production, while significantly reducing energy consumption and CO2 emissions when compared to conventional blast furnace steel produced from iron ores. However, the expansion of EAF steelmaking throughout the US and Europe directly competes with the lithium-ion battery market for scarce supplies of high-quality petroleum needle coke, the primary feedstock needed to produce state of the art graphite anode materials.. Maple Materials is developing CO2-derived alternatives to needle.